Discovering the Numerous Techniques and Technologies Behind Plastic Extrusion
The realm of plastic extrusion is a mix of accuracy, technology, and technology, pivotal to numerous sectors worldwide. Advanced machinery, electronic controls, and an array of materials merge in this complex procedure, producing high-grade, resilient items.
Understanding the Fundamentals of Plastic Extrusion
The process of plastic extrusion, commonly hailed as a cornerstone in the world of production, develops the bedrock of this conversation. Basically, plastic extrusion is a high-volume production procedure in which raw plastic product is thawed and created into a constant account. It's an approach widely utilized for producing items with a continuous cross-sectional account, such as pipelines, home window structures, and weather stripping. The process begins with feeding plastic products, commonly in the form of pellets, into a heated barrel. There, it is warmed and mixed till it comes to be molten. The molten plastic is then forced through a die, shaping it right into the wanted kind as it hardens and cools.
The Role of Different Products in Plastic Extrusion
While plastic extrusion is a typically used technique in production, the materials utilized in this process greatly affect its last outcome. Different kinds of plastics, such as polyethylene, abs, and pvc, each provide special homes to the end item. Polyethylene, known for its longevity and versatility, is commonly used in product packaging, while PVC, renowned for its stamina and resistance to environmental variables, is used in building and construction. ABS, on the various other hand, combines the ideal characteristics of both, resulting in high-impact resistance and sturdiness. The option of material not just affects the product's physical properties however also impacts the extrusion rate and temperature. Producers need to carefully think about the residential properties of the material to enhance the extrusion process.
Strategies Used in the Plastic Extrusion Process
The plastic extrusion process includes different methods that are vital to its procedure and efficiency (plastic extrusion). The conversation will certainly start with a simplified description of the essentials of plastic extrusion. This will certainly be complied with by a failure of the procedure in information and an exploration of techniques to improve the effectiveness of the extrusion method
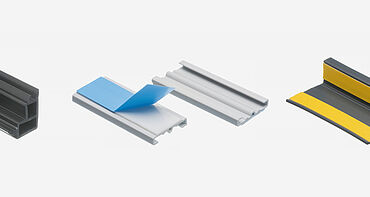
Recognizing Plastic Extrusion Essentials
In the realm of production, plastic extrusion stands as a fundamental procedure, important in the production of a wide range of everyday items. At its core, plastic extrusion involves changing raw plastic material into a continual profiled form. This is achieved by thawing the plastic, usually in the kind of granules or pellets, and requiring it through a designed die. The resulting product is a lengthy plastic piece, such as a panel, cord, or pipe finishing, that keeps the form of the die. This cost-efficient technique is highly functional, able to produce intricate shapes and accommodate a large variety of plastic products. Fundamental understanding of these essentials permits more exploration of the extra elaborate facets of plastic extrusion.
In-depth Extrusion Refine Malfunction
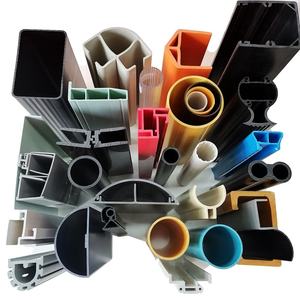
Improving Extrusion Strategy Effectiveness
Effectiveness gains in the plastic extrusion procedure can dramatically affect both the quality of the end product and the overall performance of the operation. Continuous optimization of the extrusion method is vital to keeping a competitive visit this web-site side. Strategies that boost efficiency commonly involve specific control of temperature and stress throughout the process. Modern modern technologies, such as electronic systems and sensing units, have actually contributed in achieving this control. The use of high-quality raw materials can lower waste and boost output high quality. Normal maintenance of extrusion devices can additionally reduce downtimes, hence enhancing performance. Finally, embracing lean production principles can assist remove unnecessary actions in the procedure, promoting effectiveness gains.
Just How Technology Is Changing the Face of Plastic Extrusion
The development of new technology has considerably transformed the landscape of plastic extrusion. It has led to the development of innovative extrusion equipment, which has actually improved the effectiveness and high quality of the plastic extrusion process. Innovations in the extrusion procedure have actually likewise been driven by technological advancements, supplying boosted abilities and flexibility.
Advanced Extrusion Machinery
Revolutionizing the world of plastic extrusion, progressed machinery imbued with cutting-edge technology is introducing a brand-new era of his explanation performance and accuracy. These makers, furnished with ingenious features like self-regulating temperature control systems, guarantee optimal problems for plastic processing, thus minimizing waste and improving product top quality. High-speed extruders, for example, amplify outcome rates, while twin-screw extruders supply remarkable mixing capacities, important for creating complicated plastic blends. Additionally, digital control systems provide unprecedented precision in operations, lowering human error. These devices are made for longevity, lowering downtime and maintenance prices. While these innovations are already impressive, the constant advancement of technology guarantees also higher jumps forward in the field of plastic extrusion equipment.
Technologies in Extrusion Processes
Harnessing the power of contemporary technology, plastic extrusion processes are undergoing a transformative metamorphosis. Advancements such as computerized mathematical review control (CNC) systems currently allow for even more accuracy and uniformity in the manufacturing of extruded plastic. Automation additionally enhances effectiveness, minimizing human error and labor prices. The integration of man-made knowledge (AI) and artificial intelligence (ML) formulas is changing quality assurance, predicting discrepancies, and enhancing the total efficiency of extrusion processes. With the introduction of 3D printing, the plastic extrusion landscape is also broadening into brand-new realms of possibility. These technological innovations are not just boosting the top quality of extruded plastic products but additionally thrusting the market towards an extra lasting, effective, and innovative future.
Real-World Applications of Plastic Extrusion
Plastic extrusion, a reliable and functional procedure, locates usage in numerous real-world applications. The vehicle sector additionally harnesses this innovation to create parts like plastic and trim sheet. The toughness and adaptability of plastic extrusion, coupled with its cost-effectiveness, make it a crucial procedure throughout numerous sectors, highlighting its widespread useful applications.
The Future of Plastic Extrusion: Patterns and forecasts
As we look to the perspective, it comes to be clear that plastic extrusion is poised for considerable advancements and improvement. Environment-friendly alternatives to standard plastic, such as bioplastics, are additionally anticipated to gain traction. These fads indicate a vibrant, evolving future for plastic extrusion, driven by technological technology and a commitment to sustainability.

Conclusion
In conclusion, plastic extrusion is a complex procedure that utilizes sophisticated technology and varied products to produce varied items. Technological improvements, such as digital controls, enhance the production procedure and make certain consistent results. In addition, the industry's focus on sustainability and intelligent machinery suggests a promising future. As plastic manufacturing remains to evolve, it continues to be an important part of lots of industries worldwide.
In essence, plastic extrusion is a high-volume production procedure in which raw plastic product is melted and created right into a continual account.While plastic extrusion is a frequently utilized technique in manufacturing, the products used in this process significantly affect its last outcome. At its core, plastic extrusion involves changing raw plastic material into a continuous profiled form. It has led to the development of innovative extrusion equipment, which has enhanced the efficiency and quality of the plastic extrusion procedure.In final thought, plastic extrusion is a complex procedure that utilizes innovative innovation and varied products to create varied products.